VTScada Partner: ElectroMechanica
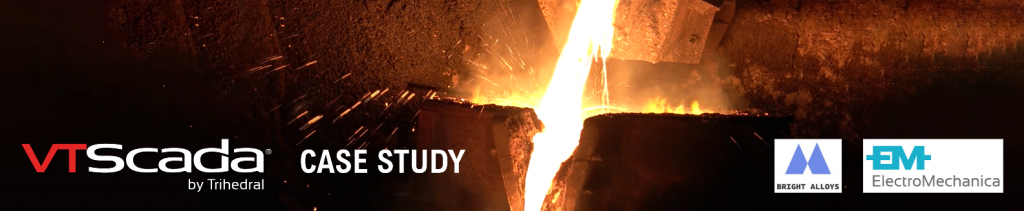
Metallurgy is by nature a dangerous, highly energy-consuming, and capital-intensive industry, yet currently its biggest difficulty lies in automation. Embracing the global smart manufacturing trend, the metallurgical industry is actively seeking efficient monitoring and control upgrades on production lines.
South Africa has developed a thriving metallurgical industry thanks to its rich chromium deposits, a key ingredient in stainless steel production. SCADA System VTScada emerged as a transformative solution amid the challenges faced by Bright Alloys, a ferrochrome smelter in South Africa. Due to the difference in timelines and technologies involved in facility construction, Bright Alloys encountered difficulties in equipment integration and expansion. Additionally, establishing resilient redundancy systems is critical for continuous processing. Furthermore, the lack of real-time insight into production lines often requires additional resources to deal with downtime issues.
To address these pain points, VTScada was implemented with the support of Delta’s authorized distributor ElectroMechanica (www.em.co.za). In only three weeks, EM seamlessly integrated diverse systems, establishing an efficient monitoring and control system at Bright Alloys. VTScada’s driver library supports various communication protocols, enabling the integration of Delta’s PLC AH500 on the production line. This integration resulted in a big leap in production efficiency, reducing feed rate tolerance to within 1%. The built-in Historian database facilitates bi-directional synchronization and data traceability. This feature allows operators to retrospectively review equipment information and identify anomalies through a visualized interface, enabling prompt issue detection.
Metallurgical plants generate extreme heat and toxic fumes, which may hinder close monitoring by operators. As a result, real-time monitoring of furnace temperature is difficult to carry out. Bright Alloys once experienced a catastrophic event a furnace burn-through that caused unexpected downtime and negative productivity impact. It happened when a rapid temperature increase in the furnace went unnoticed by the operator. To nip similar problems in the bud, VTScada’s Idea Studio creates a clear monitoring interface with widget extensions, showing furnace hot spots in real-time. With system anomaly reports, operators can make prompt and well-informed decisions.
SCADA System VTScada offers the following benefits:
• Driver Library for Diverse System Management – Supports 120+ industry communication standards and proprietary protocols without installing additional modules, ensuring cost savings and easy integration of existing systems. Provides third-party data-sharing communication interfaces, such as ODBC Server, OPC Server, and WEB Services, to ensure standardization.
• Robust Redundancy and Alarm System for Swift Response – Offers hot standby, system server failover, historical records synchronization, and alarm databases. Diverse notification channels are available for instant fault reports.
• Real-Time Remote Monitoring for Efficient 24/7 Management – Provides system information in real-time, such as energy consumption and power quality, eliminating the need for manual meter readings and allowing timely adjustments. Impressively, VTScada helped Bright Alloys reduce natural gas consumption by a third.
VTScada has brought a fresh perspective into factory monitoring and control. Not only does it boost production efficiency, but it also enables the metallurgical industry to manage resources precisely. VTScada has much more to offer than productivity enhancement, it stands as a powerful automation engine propelling factories forward.